Technological systems
The purpose of the Technological systems component is to support students to develop logical capabilities, by understanding why and how systems work the way they do, then to apply this knowledge when they design and develop their own systems.
A technological system is a set of interconnected components that has been designed to fulfil a particular function without further human design input.
Technological systems transform, store, transport, or control materials, energy, and/or information for a particular purpose.
A door mechanism is an example of a system made of material parts that are controlled to allow a door to open and close. Computer code is an example of an information system where the lines of code direct the computer to carry out instructions. Generating power using hydro-electricity is an example of a system that controls and transforms the energy of moving water into electricity.
In any system, how the parts work together is as important as their individual characteristics.
In order for students to design their own systems, it is important they understand systems concepts:
- input, output, transformation, and control
- "black box”
- redundancy and reliability
- operational parameters.
Key ideas
Products and systems
Technological outcomes can be products and/or systems (see Characteristics of technological outcomes), but in this component the focus is on outcomes as systems.
Inputs
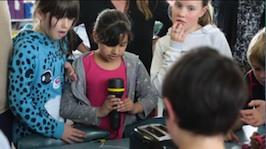
The specialised knowledge required to develop or understand a particular type of technological system (for example, biotechnological or electronic control) will vary greatly, but the same concepts underpin all systems: inputs (for example, raw materials, information or energy) are transformed into outputs in a controlled manner.
A system may of course need operator input to fulfil its purpose, but this input does not alter the design of the system (or therefore its function). For example, the driver of a car has to press a pedal (human input) to apply the brakes, but the brakes (a technological system) work without any design input from the driver (it is already fully designed).
Some systems (for example, pop-up toaster, camera or heat pump) require the user to select appropriate settings (operator input), but once this has been done the system functions exactly as it was designed to do. Similarly, a system may require the human operator to make quality control judgments, in which case they change the settings but not the design of the system.
Outputs
All technological systems produce an output, the intended outcome. For example, the intended outcome of a system designed to manufacture chocolate Easter eggs is the eggs; the intended outcome of a telephone communication system is transformed and transported information (a voice in another location); the intended outcome of a wind-based generation system is transformed energy (electricity). But most technological systems also produce other outputs such as heat, noise, gases, chemical by-products, and waste materials, which are often sources of pollution. These may or may not have been foreseen when the system was being developed.
Transformations
Transformations are the processes within a system that convert inputs into outputs in a controlled and intended way without further human design input.
Simple technological systems change inputs into outputs via a single transformation.
Subsystems
More complex systems often contain subsystems which can be thought of as systems within a system.
For example, a car braking system is a subsystem of the vehicle system. Subsystems can be thought of as components of the whole, each having a specific function that supports the overall functioning of the system and enables it to achieve its intended purpose.
The key properties of a subsystem are the particular transformation for which it is responsible and how it is integrated into the whole. A subsystem’s role can be determined by examining how inputs change to outputs in that part of the system. Effective interfaces between subsystems are critical if the overall system is to function successfully.
Control
Control mechanisms are designed to enhance the efficiency of a technological system by maximising desirable outputs and minimising undesirable outputs.
Some systems have self-regulating control mechanisms built into them; these monitor and adjust the various transformations in response to changing inputs to ensure that the outputs are consistent in kind and quality.
Unlike self-regulating systems, intelligent systems are designed to respond to environmental inputs by changing their components and/or transformation processes, possibly in unforeseen ways, to produce unspecified (but hopefully desirable) outputs.
Operational parameters
All systems have operational parameters – boundaries and/or conditions within which they have been designed to function. Operational parameters are closely related to the concepts of redundancy and reliability, both of which influence the design and performance of systems.
When budgets are tight, designers can find themselves under pressure to sacrifice redundancy and reliability (performance is not always the only priority in system design) to save costs, potentially raising ethical, cultural, moral, and environmental issues.
Redundancy and reliability are important considerations when determining whether a technological system is fit for purpose.
Redundancy
In technological systems, redundancy means “allowing a bit extra” – providing more time, information, and/or resources than is strictly necessary for a system’s successful functioning. Redundancy allows faults to be tolerated or detected before the system fails in some way. One example of redundancy is the use of components made to higher tolerances than are necessary to meet fitness-for-purpose criteria.
While redundancy may provide additional capability, often in the form of increased safety margins, it can also result in “over-engineering”, when systems contain components that have capabilities that will never be required. System engineers try to eliminate such redundancy because it introduces unnecessary complexity and often impacts on a system’s ability to function as specified (for example, production costs are too high).
When developing complex systems it is important that designers have a broad understanding of redundancy so that they can take all the variables into account when making decisions.
Reliability
In this context, reliability means the likelihood that a system or sub-system will perform as intended under specified conditions for a given period of time. It is therefore something that is built into the overall design of a system and its constituent parts. Tolerances for reliability are specific to a system and relate closely to the type of output. For example, if human safety depends on the output, reliability tolerances will be very stringent.
When a technological system stops functioning successfully it will be for one of three reasons: malfunction, gradual loss of functioning due to ongoing use (wear and tear), or designed failure (see Characteristics of technological outcomes). In all three cases reliability is the issue.
Black box
When describing technological systems, the term black box is often used to denote a hidden process or series of processes by which inputs are transformed into outputs. This practice has its advantages and disadvantages.
One advantage is that it allows complex systems to be explored and understood in a holistic sense, without having to delve deeply into technicalities. Another is that it allows systems to be designed in such a way that a technician with limited knowledge can replace a failed component (for example, a circuit board) with minimal disruption. Designing a system for easy maintenance increases some costs (components will be replaced rather than repaired) but reduces others (maintenance is quicker and can be done by less skilled personnel).
A major disadvantage of black boxing is that it makes the detail invisible and, therefore, not amenable to being understood. This can cause difficulties when modifications and/or development are required. It can also disempower users, who are unable to diagnose the cause of problems or attempt to solve them.
Note that some modern transport systems (cars, trucks, trains, airplanes) contain ‘black boxes’ which can record details of journeys, accidents, and monitor servicing needs. These black boxes should not be confused with the black box concept described here.
Representations
Technological systems are often represented in diagrammatic form, with symbols for the various components. Here is a basic example:
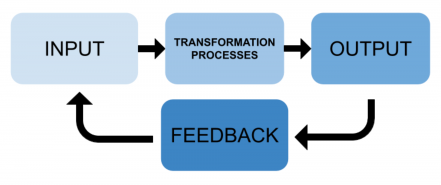
While some symbols are common to all systems (for example, arrows to denote direction), specialised languages play a vital role in the development and communication of technological systems. Design concepts can be represented using different communication tools such as flow diagrams, network diagrams, and 3-D models. These can be used to explore and understand relationships between the parts of a system or between different systems.
Different technological communities often supplement or modify existing symbols to communicate details of systems – for example, components, layout or connections – in specialised diagrams/representations.
Technological systems: Key ideas (Word 2007, 31 KB)
Acknowledgment: This paper is derived from an earlier version by Dr Vicki Compton and Cliff Harwood.